动力电池模组线:
在动力电池模组自动化装配的过程中,原有的半自动化生产线已越来越不能满足电池生产厂商高自动化节拍的需求,原有需要人工堆放电芯,涂胶的工作越来越成为生产的瓶颈。
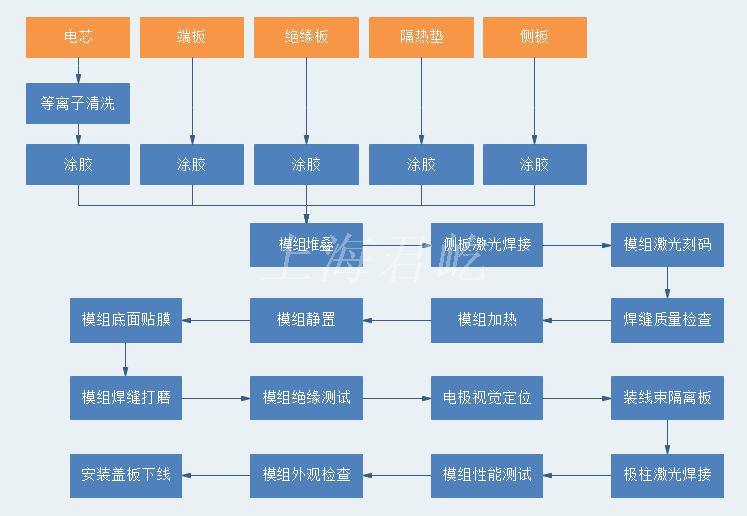
为此上海君屹潜心研发了高生产节拍的智能化装配生产线,包含组件上料,清洗,涂胶,模组堆叠,侧板涂胶,模组侧缝CMT焊/侧缝激光焊,模组激光刻码,模组加热,模组贴膜,模组静置,极柱激光焊接,焊缝打磨,模组自动下线。关键工位实现全自动化生产,可实现多种产品的柔性生产,兼容模组尺寸工艺类型多。
1.多工艺兼容:侧缝焊接兼容CMT弧焊与激光焊两种焊接工艺,可实现快速切换。
视觉定位系统:电池模组装配后,往往尺寸公差较大,很难达到激光加工对间隙位置尺寸要求,导致加工质量急速下降,视觉定位系统的导入则能满足精准定位的需求,一般精度可达到±0.05mm以上,通过视觉拍照数据采集,并将来料偏差反馈给控制系统,从而实现了加工位置的高精度定位。
2.视觉跟踪系统:由于电池模组每个焊接位置高度不可能做到完全一致,焊接时,会导致虚焊、爆焊的发生,其焊接品质很难保证。必须配备高度跟随系统,即在每个焊接位置,焦距调节轴能够做到微调使激光焊接头固定在焦距位置。
采用视觉寻址+激光测距,寻址模组极柱位置,其中视觉相机定位极柱X,Y方向尺寸偏差,激光测距确定极柱Z向尺寸偏差,并将偏差值反馈给激光焊接头,保证焊接质量,同时采用激光测距检查极柱面平面度,提高设备合格率。
3.多产品自适应系统:不同种类规格尺寸的电芯在堆叠成不同尺寸的模组后,每经过一道工序都需要适配自适应系统来确保整线节拍的联动,尤其是焊接工序,只有适应不同尺寸的模组才能完成模组PACK工序。自适应系统加载必要的伺服切换系统,实施产品加工区域内位置根据产品来料自动切换定位,可不受任何形式来料的限制,完成焊接工作并传送到下一道工序。 4.焊后智能检查:使用人工对焊缝外观检查,判断依据比较客观,需凭经验,判断依据难数据化,易误判,使用激光轮廓扫描仪+CCD相机,收集焊缝的三维信息,颜色信息,将判断依据数据化,检查焊缝长宽高,颜色,判断是否焊穿,断弧,有气孔,焊缝变色,由设备自动判断焊缝是否合格,并将采集的焊缝信息上传到MES,方便以后查询。
5.MES管理系统:整条线体具备制造数据管理、计划排产管理、生产调度管理、库存管理、质量管理、工作中心、物料管理、生产过程控制、底层数据集成分析、上层数据集成分解等管理模块。整线能实时监控产品生产过程的生产及测试数据,且数据能准确无误的追溯并存储。整线配置服务器控制台以及大屏幕显示功能,实行智能制造与数字化企业平台。